Revolutionizing Manufacturing with 3D Printing Prototypes
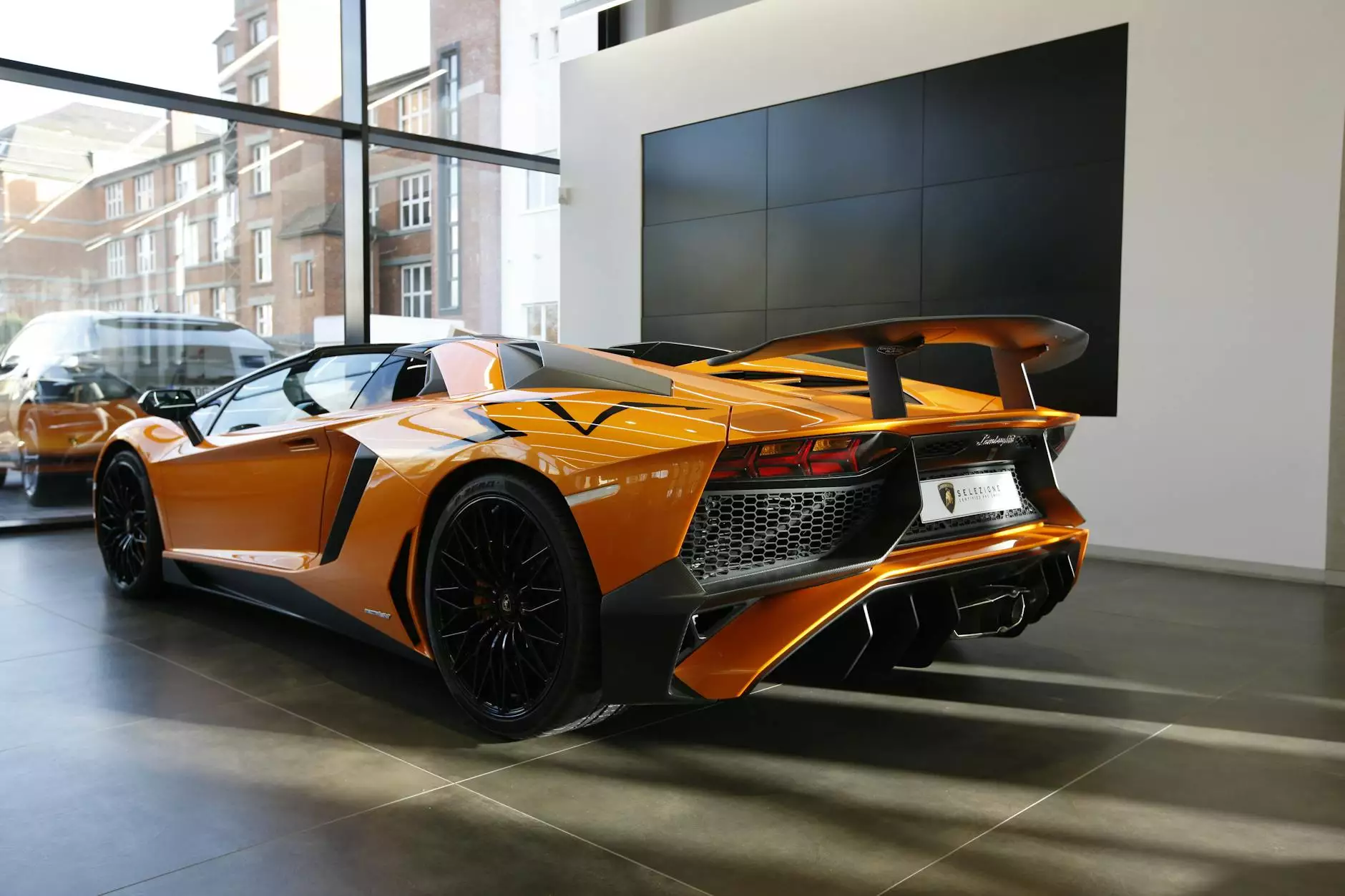
In the ever-evolving world of manufacturing, 3D printing prototypes have emerged as a game-changer. This cutting-edge technology is not only reshaping how products are developed but also enhancing the way businesses, particularly in the metal fabrication industry, operate. With its ability to quickly convert digital models into tangible objects, 3D printing is driving innovation, streamlining production processes, and enabling businesses to respond swiftly to market demands.
Understanding the Basics of 3D Printing Prototypes
Before diving deeper, it’s crucial to understand what 3D printing prototypes entail. At its core, 3D printing—also known as additive manufacturing—is a process that creates three-dimensional objects layer by layer from a digital file. This technology allows manufacturers to produce prototypes rapidly, enabling faster product development cycles and innovative design iterations.
The Process of Creating 3D Printing Prototypes
1. Designing the Model
The first step in creating a 3D printing prototype involves designing the model using CAD (Computer-Aided Design) software. This step is crucial as it determines the accuracy and functionality of the prototype. Designers can incorporate intricate details and specifications, enhancing the prototype's usability in real-world applications.
2. Selecting the Right Materials
Choosing the appropriate material for prototyping is essential. Different materials affect the quality and properties of the final product. Common choices include:
- PLA (Polylactic Acid): Excellent for simple prototypes due to its easy handling.
- ABS (Acrylonitrile Butadiene Styrene): Known for durability, making it ideal for functional prototypes.
- Metal: For high-end applications, metal 3D printing provides strength and durability necessary for functioning parts.
3. Printing the Prototype
This step involves the actual 3D printing, where the designed model is produced layer by layer. High-precision printers utilize techniques such as FDM (Fused Deposition Modeling), SLS (Selective Laser Sintering), or DMLS (Direct Metal Laser Sintering) to bring designs to life.
4. Post-Processing
After printing, components may require post-processing, which can include:
- Sanding: To smooth out surfaces.
- Painting: For aesthetic finishes.
- Heat Treatment: To enhance material properties.
The Benefits of 3D Printing Prototypes in Metal Fabrication
1. Cost-Effectiveness
One of the most significant advantages of using 3D printing prototypes in metal fabrication is the cost savings. Traditional manufacturing methods often involve expensive tooling and lengthy setup times. In contrast, 3D printing significantly reduces costs associated with prototyping by eliminating the need for expensive molds and allowing for immediate production adjustments.
2. Speed and Efficiency
In today's competitive market, speed is paramount. 3D printing enables manufacturers to produce prototypes in days rather than weeks. This rapid turnaround allows businesses to test concepts, gather feedback, and make necessary modifications efficiently, ensuring they stay ahead in innovation.
3. Enhanced Design Flexibility
3D printing prototypes allow for intricate designs that may be impossible or cost-prohibitive with traditional manufacturing methods. Complex geometries and lightweight structures can be easily realized, enabling engineers to push the boundaries of design and functionality.
4. Sustainability
As businesses seek to reduce their environmental impact, 3D printing presents a more sustainable solution. With additive manufacturing, material waste is significantly minimized since only the required material is used to create the prototype. Additionally, many 3D printing materials are recyclable, further enhancing sustainability efforts.
Applications of 3D Printing Prototypes in Various Industries
The versatility of 3D printing prototypes extends across numerous industries, including:
- Aerospace: Quick prototyping of components and parts that can be rigorously tested.
- Automotive: Rapid prototyping of car models, reducing the time from concept to production.
- Healthcare: Customization of medical devices and implants, tailored to individual patient needs.
- Consumer Products: Quick turnaround on designs for testing market viability and consumer feedback.
Challenges and Considerations in 3D Printing Prototypes
1. Material Limitations
Despite its many advantages, 3D printing prototypes do have material limitations. Not all materials are suitable for every application, and the properties of 3D printed materials can differ from traditionally manufactured materials.
2. Technology Costs
The initial investment in high-quality 3D printing machinery can be substantial. However, companies that view this technology as a long-term investment can see significant returns through efficiency gains and cost savings.
3. Skill Gap
The implementation of 3D printing requires specific knowledge and skills. Organizations must invest in training their workforce to take full advantage of this technology's capabilities.
The Future of 3D Printing Prototypes in Metal Fabrication
The future of 3D printing prototypes looks bright, especially in the metal fabrication sector. As advancements continue, we anticipate:
- Improved Materials: Development of new alloys and composites designed specifically for 3D printing.
- Increased Adoption: More businesses embracing additive manufacturing as a standard practice.
- Integration with AI and IoT: Enhanced efficiencies through smart manufacturing processes.
Conclusion
In conclusion, 3D printing prototypes are at the forefront of a manufacturing revolution, especially within the realm of metal fabrication. The benefits of this innovative technology—from cost savings to enhanced design capabilities—make it an invaluable asset for businesses looking to innovate and thrive in a competitive landscape. As technology progresses, embracing 3D printing can provide companies a significant edge, setting the stage for unimaginable possibilities in product development and manufacturing efficiency. As noted on DeepMould.net, integrating cutting-edge manufacturing solutions like 3D printing can elevate a business's potential to operate effectively in an ever-changing market.